Top 3 Methoden, um Millionen zu verlieren, Optimierung der Bestände
- -
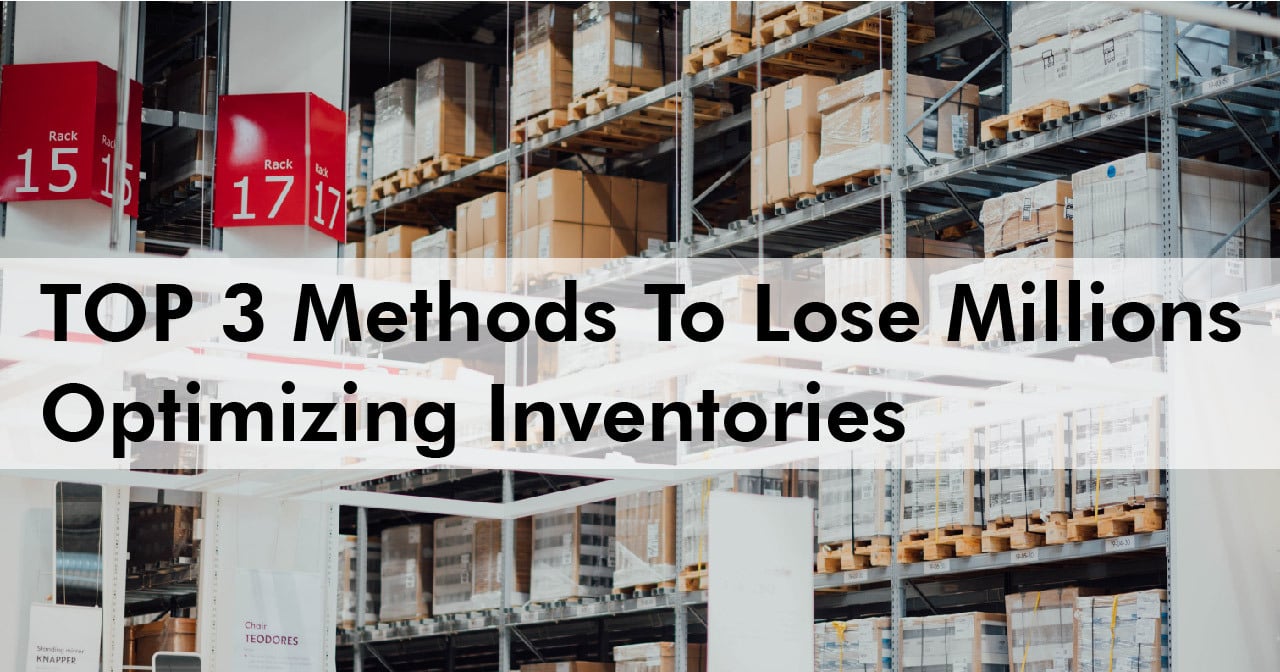
5 Minuten zum Lesen
Inhaltsverzeichnis:
- Einführung
- 1. Min/Max-Bestandsbestellsystem verwenden
- 2. Verwenden Sie das Nachbestellsystem für feste Zeiträume
- 3. Verwendung von dynamischen Meldebeständen und Sicherheitsbeständen auf der Grundlage von Prognosemodellen
- Testen Sie ein System, das die Bestandsoptimierung richtig macht
Einführung
Der Autor dieses Artikels befragte über 500 Unternehmen, die sich gleichzeitig über Lagermangel und übermäßige Lagerbestände beschwerten. In ihrem Fall scheiterten die klassischen Strategien zur Auffüllung der Lagerbestände ohne erkennbaren Grund. Dies ist das erste Mal, dass wir unsere Notizen darüber teilen, was bei den klassischen Bestandsoptimierungsansätzen schief gelaufen ist, und wir hoffen wirklich, dass Sie sie langweilig finden werden, weil Sie diese Fehler nie machen.
Um sicherzustellen, dass wir auf der gleichen Seite stehen, beachten Sie bitte, dass sich der Artikel an leitende Positionen in der Lieferkettenplanung oder im operativen Bereich richtet. Der Artikel erklärt, wie Lagerbestandsplaner klassische Strategien zur Verwaltung von Lagerbeständen anwenden und ohne offensichtlichen Grund Fehlmengen oder übermäßige Bestände nicht reduzieren können. Bitte übertragen Sie keine Fehler auf Ihr Bestandsplanungs- und Einkaufsteam, bevor Sie nicht den gesamten Einkaufsprozess eingehend geprüft haben.
Unternehmen, die Tausende von Produkten oder Komponenten verwalten, haben immer mit einem Kompromiss zwischen Lagerbestand und Servicelevel zu kämpfen. Sie verringern die Lagerbestände, um die Frachtkosten zu senken, aber das verringert die Produktverfügbarkeit und umgekehrt.
Die Lagerbestände scheinen unter Kontrolle zu sein, während ein Unternehmen mit über 30 Jahren Betriebszugehörigkeit einen Guru der Lagerauffüllung hat, der die Verkaufszahlen und Artikel, die gut im Trend liegen werden, vorhersieht und die Faustregel erfolgreich zur Produktion von Auftragsmengen nutzt. Doch früher oder später stellt sich bei einer externen Prüfung heraus, dass die Lagerumschlags- und Füllrate im Vergleich zu anderen Unternehmen der Branche so schlecht ist. Also beschließt das Unternehmen, ein glänzendes neues automatisiertes Lagerauffüllsystem zu implementieren, das eine Reihe von klassischen Ansätzen verwendet, die sich als Industriestandard erwiesen haben.
Und was für eine Überraschung würde eine gute 60% der Unternehmen erwarten, nachdem sie ihre Lagerbestände in 3-6 Monaten nach Einführung des Lagerauffüllungs- und Optimierungssystems bewertet haben. Sie enden dort, wo sie in Bezug auf Bestandsverzerrungen angefangen haben, und das einzig Gute daran ist, dass das System dem Planungsteam die meiste Zeit die Möglichkeit gibt, sich zu entspannen, aber das ist nicht in jedem Implementierungsfall auch so.
Was sollten Sie also auf branchenübliche Weise tun, um diese frustrierende Erfahrung unweigerlich zu wiederholen? Hier ist eine Liste der Top-3-Ansätze:
1. Min/Max-Bestandsbestellsystem verwenden
Hierbei handelt es sich um eines der grundlegenden Bestandsplanungssysteme, das oft direkt in Ihr ERP-System integriert ist. Es gibt eine Menge Informationen darüber, wie diese Strategie funktioniert - Sie können leicht viele Handbücher und Artikel, in denen erklärt wird, wie man die Min- und Max-Stufen feinabstimmt.
Bleibt nur noch eine Frage: Würden Sie, wenn für ein Produkt oder Material ein Nachschubalarm auftritt, den Kauf noch am selben Tag ausführen oder einige Wochen warten, um dieses Produkt mit allen anderen Produkten dieses Lieferanten zu synchronisieren, um die Transportkosten zu minimieren und die Mindestabnahmeforderungen des Lieferanten zu erfüllen?
Wenn Sie die Frage bekommen haben, denken Sie eine Weile darüber nach. Aber es ist ein Haken - beides funktioniert nicht. Sie wählen buchstäblich zwischen einem zweiwöchigen Stockout und einem Kapitalstopp für einen unbekannten Zeitraum. Praktisch tun Planer das in allen möglichen Kombinationen - einige kaufen sofort ein, was die Transportkosten erhöht und einen Überbestand schafft, und andere ignorieren die potenzielle Knappheit, während die nächste große Bestellung aufgegeben werden muss. Im letzteren Fall erzeugt der Planer periodische Engpässe bei verschiedenen Produkten in jeder Bestellung bei jedem Lieferanten.
Einige Unternehmen verstehen das Thema Min/Max von Anfang an und ziehen es daher vor, mit dem Ansatz #2 auf eine differenziertere Art und Weise Geld zu verlieren.
2. Verwenden Sie das Nachbestellsystem für feste Zeiträume
In Kürze haben wir hier die 2-wöchige Stockout-Option aus Fall #1 vorselektiert.
Lassen Sie mich erklären. Das festgelegte Periodensystem löst einmal pro Periode, z.B. eine Woche oder einen Monat, Bestellungen aus. Und das scheint besonders bei Bestellungen im Ausland sinnvoll. Aber raten Sie mal, was mit Artikeln passiert, die sich schneller verkaufen, als wir erwartet haben. Sie werden bis zum nächsten Zyklus ignoriert, das ist bedauerlich.
Oh, warten Sie, es gibt wahrscheinlich eine Lösung für Engpässe. Einige Unternehmen legen Sicherheitsbestände im Wert von 90 Verkaufstagen an, um sicherzustellen, dass es nie wieder zu Engpässen kommt. Unabhängig davon, dass die jährlichen Lagerhaltungskosten um ein paar Millionen Dollar in die Höhe schnellen werden. Dann handelt es sich hier um eine Bestandsdeoptimierung, oder was wäre eine gute Definition dafür?
3. Verwendung von dynamischen Meldebeständen und Sicherheitsbeständen auf der Grundlage von Prognosemodellen
Genau wie traditionelle Annahmen, die auf durchschnittlichen Verkäufen basieren, bringt Sie die Prognose unter Berücksichtigung aller möglichen Parameter nicht näher als eine Genauigkeit von 50-60%. Das bedeutet 40-50% für die Zeit, in der Sie sich auf Sicherheitsbestände verlassen, was wiederum ein Kompromiss ist - wenn Sie den Sicherheitsbestand verringern, gehen Ihnen Einnahmen verloren, wenn Sie ihn erhöhen, steigen die Frachtkosten und das Kapital wird eingefroren. Noch einmal dasselbe Problem - ein Unternehmen optimiert die Lagerbestände und verliert weiterhin Millionen pro Jahr.
Testen Sie ein System, das die Bestandsoptimierung richtig macht
Sie fragen sich wahrscheinlich, was überhaupt anders gemacht werden kann. Unten sehen Sie einen Spoiler.
Ja, es gibt eine Methode, um Bestandsoptimierung richtig zu machen, auch wenn Sie eine Weile brauchen werden, um sie zu verstehen. Die Methode beginnt mit der Berücksichtigung variabler Einkaufszykluszeiten und variabler Einkaufsmengen. Das System mit der Methode sollte darauf vorbereitet sein, jederzeit eine Bestellung zu erteilen, die den Einkaufsbeschränkungen entspricht, wenn die tatsächlichen Bedarfszahlen plötzlich stark vom Plan abweichen. Wenn das System stabil arbeitet und keine Probleme hat, können Sie mit viel geringeren Lagerbeständen als Ihre Konkurrenten arbeiten, Ihren Kunden ein höheres Serviceniveau bieten und viel schneller wachsen als Ihre Konkurrenten.
Erfahren Sie mehr über eine bessere Methode, um Verluste in Ihrer Lieferkette zu stoppen.
- Prognostizieren, planen und bestellen Sie doppelt so schnell.
- Reduzieren Sie Lagerbestände um bis zu 98% und die Einnahmen entsprechend erhöhen.
- Reduzieren Sie überschüssige Bestände um 15-50%.
- Erhöhung des Lagerumschlags um 35%.
Keine Kreditkarte erforderlich.
Weitere Lektüre:
- Wie man mit Lieferkettenprozessen während des Coronavirus-Ausbruchs umgeht
- Warum von Excel auf Bestandsplanungssoftware umsteigen?
- Muss gelesen werden: Intelligente Supply-Chain-Management-Lösungen zur Optimierung von Geschäftsprozessen
- Funktionsübergreifende Ausrichtung in der Supply Chain Planung: Eine Fallstudie zur Vertriebs- und Betriebsplanung [PDF]
- Nachfrage- und Angebotsmanagement: Kollaborative Planung, Vorhersage & Nachschub
Verlassen Sie sich bei der Planung immer noch auf manuelle Arbeit in Excel?
Automatisieren Sie noch heute die Nachfrage- und Angebotsplanung mit Streamline!
- Erreichen Sie eine optimale Lagerverfügbarkeit für 95-99%+ und stellen Sie sicher, dass Sie die Kundennachfrage stets erfüllen können.
- Erreichen Sie eine Prognosegenauigkeit von bis zu 99% und profitieren Sie so von einer zuverlässigeren Planung und Entscheidungsfindung.
- Reduzieren Sie Lagerbestände um bis zu 98% und minimieren Sie so verpasste Verkaufschancen und Kundenunzufriedenheit.
- Reduzieren Sie überschüssige Lagerbestände um bis zu 50% und geben Sie so wertvolles Kapital und Lagerraum frei.
- Erhöhen Sie die Margen um 1–5 Prozentpunkte und steigern Sie so die Gesamtrentabilität.
- Profitieren Sie innerhalb eines Jahres von einem bis zu 56-fachen ROI, wobei in den ersten drei Monaten ein ROI von 100% erreichbar ist.
- Reduzieren Sie den Zeitaufwand für Prognosen, Planungen und Bestellungen um bis zu 90%, sodass sich Ihr Team auf strategische Aktivitäten konzentrieren kann.