失敗例から学ぶ: 在庫最適化で数百万ドル失うための上位3つの方法
–
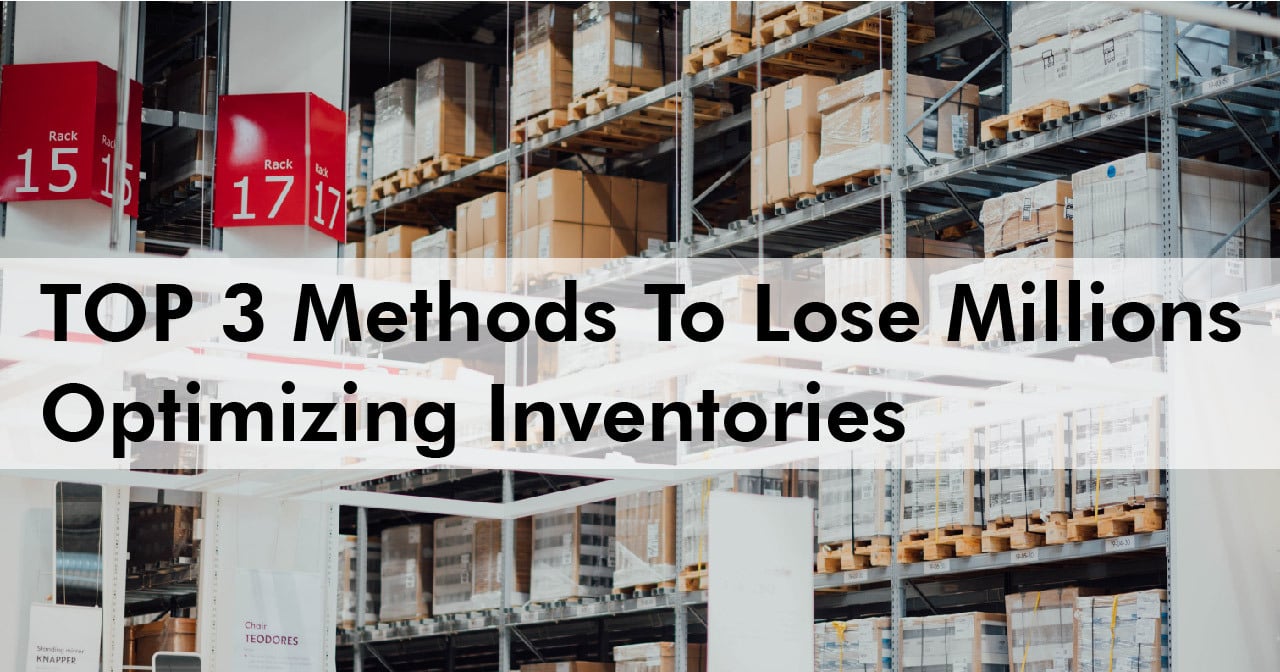
およそ5分で読めます
目次:
- はじめに
- 1. Min/Max在庫注文システムの利用
- 2. 発注間隔一定の在庫注文システムの利用
- 3. 予測モデルに基づいた動的発注点と安全在庫を併用する在庫注文システムの利用
- 在庫最適化を適切に行うシステムを試してください
はじめに
筆者は、これまでに欠品と過剰在庫の両方に悩みを抱える500社以上の企業にインタビューしてきました。これらの企業では、もっともらしい理由もなく、古典的在庫補充アプローチで失敗をしていました。古典的在庫補充アプローチで失敗した点を公開するのは、これが初めてです。読者の皆様がこの内容から多くを学び、失敗をしないことを心から願っています。
さて筆者と読者の皆様が共通の目的を持っていることをはっきりさせるため、サプライチェーン計画やその業務を担当する経営幹部や管理職に向けた記事であると、ここで説明しておきたいと思います。この記事では、在庫計画担当者の古典的アプローチの適用方法を説明したのち、いかにして欠品・過剰在庫対策に失敗したのかを説明します。管理職の皆様へお願いがあります。購買プロセス全体の詳細調査をせずに、これら説明する失敗例を皆様のシステムや計画・購買担当チームに無理やり適用しないでください。必ず自社の購買プロセスを確認してください。
数千単位の製品やコンポーネントを扱うビジネスの世界では、在庫水準とサービスレベルの間でトレードオフがあり、このトレードオフと格闘しています。在庫管理費用を下げるには、在庫水準を下げればよいのですが、同時にサービス率も低下してしまいます。逆も同じで、サービス率を上げると、管理費が増大してしまいます。
ここで架空の会社を想定し、在庫システム導入までの経緯を紹介します。この会社には、在庫補充・在庫計画の経験が30年以上のベテランが在籍しており、そのベテランが売れ筋の売り上げの数字と品目を予測し、経験則から購入オーダを予測しています。このような好調な会社でも、その在庫回転率や充足率が業界他社よりも非常に低いと、外部監査から遅かれ早かれ判明してしまいます。そこでこの会社は、業界標準として証明された一連の古典的アプローチがたっぷりと詰まった自動在庫補充システムの導入を決定したと仮定します。
失敗例の詳細はここからです。在庫システム導入してから、3か月から6か月以内経過したとします。その後企業はシステムを評価するのですが、その企業の60%に起こりうることは何でしょうか?残念なことですが、在庫水準を減らすどころか、在庫水準が乱れただけでした。導入システムが安定していたのは唯一の救いでしたが、それでもすべての機能が安定していたわけではありません。
このような失敗が繰り返されている、標準的な方法を紹介いたします。よくある失敗例の上位3つを紹介します。
1. Min/Max在庫注文システムの利用
Min/Max在庫注文システムは基本的な在庫計画システムの1つです。カスタマイズしていないERPシステムでも、たいてい用意されている機能です。在庫水準の最小値と最大値を調整し発注する戦略ですが、多く文献でその機能が説明されています。 Min/Max在庫水準調整方法の紹介記事.
多くの文献を読んでも、疑問点が残りますよね。発注点を割り込んだ品目に、発注オーダーを発行するのはわかります。しかし、品目別に個別発注したらよいのでしょうか? 輸送コストを抑えるため、複数品目の一括発注すべきでしょうか? 一括発注するには、発注タイミングをどれほどずらせばよいのでしょうか?数週間でしょうか? 数か月でしょうか? サプライヤーの最低発注条件があったらどうしますか?
ここから読み進める前に、どのようにすべきか少し考えてください。でもこれは、ちょっとしたひっかけ問題です。実は、個別発注・一括発注のどちらでも機能しません。発注タイミングを遅らせば、欠品が発生し、早めれば財務評価を悪くします。実際の業務では、計画担当者は考えられる組み合わせで、発注をしています。個別発注の場合、輸送コストが増え過剰在庫になります。次回一括発注のために、発注量を減らして、欠品の可能性を黙認する計画担当者もいます。一括発注の場合、サプライヤーの取り扱い品目で定期的な欠品につながります。
このようにMin/Max在庫の問題がありますが、一部の企業ではこの問題に事前に対処しています。対処方法は、Min/Max在庫よりも少し複雑ですが、それでも依然としてお金を無駄にしています。次の失敗例を紹介します。
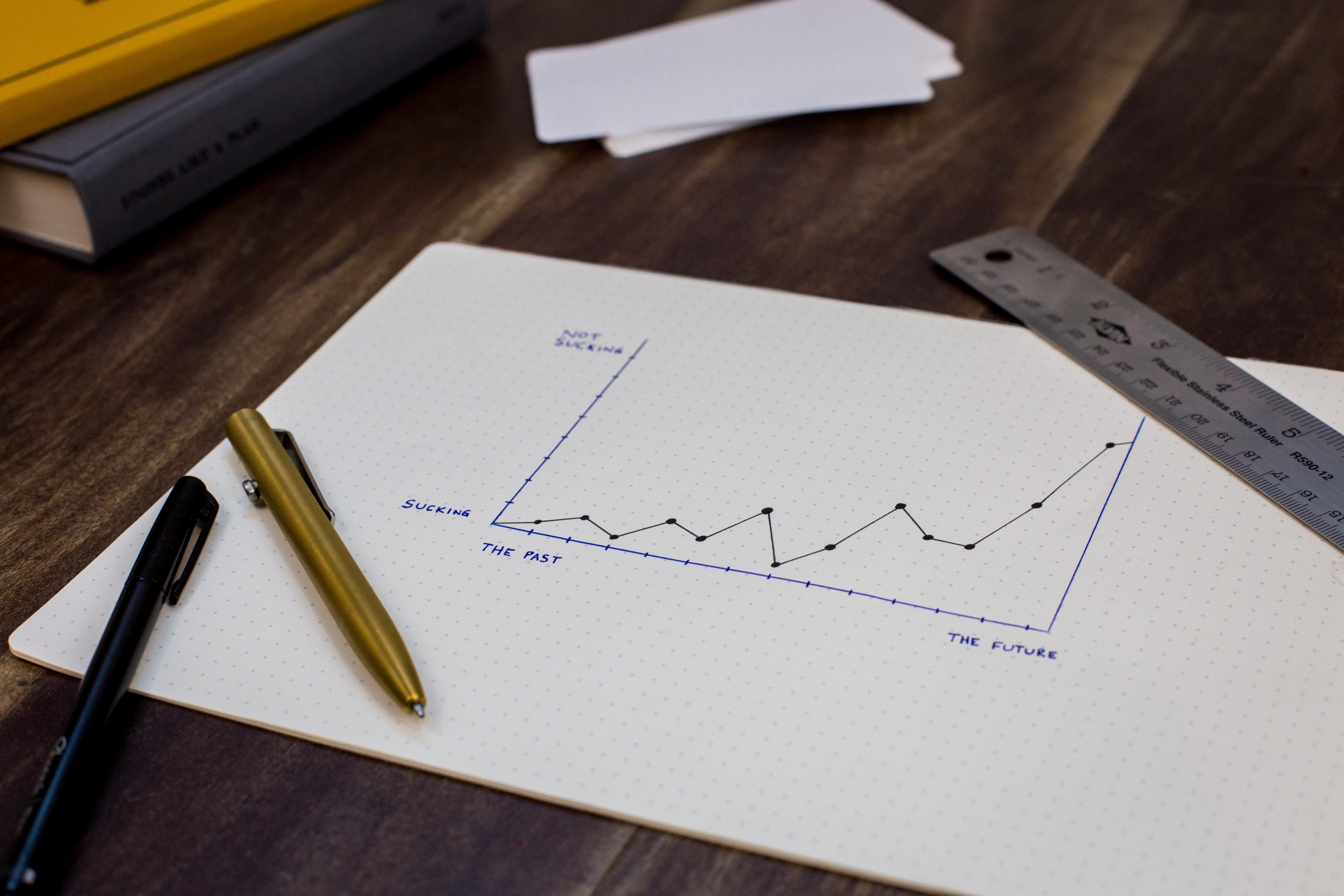
2. 発注間隔一定の在庫注文システムの利用
これまではケース1のみが選択肢でしたが、2週間の欠品が選択肢に追加されます。
これについて説明します。定期発注システムは、週次や月次などの一定周期で、購買オーダーを1回発行します。船便などを利用した海外注文などでは、非常に合理的と思えますね。もし、オーダー発行の周期よりも、早いペースで販売される人気商品があったらどうでしょうか? 残念ながら、次のサイクルまで購買オーダーは作成されません。つまり欠品になります。
でも安心してください。欠品の解決策があります。安全在庫です。お金持ちな企業であれば、十分な量の安全在庫を持てるかもしれません。そんな企業であれば、90日分の在庫でも気にしないと思います。年間では数百万ドル以上の費用が加算されるかもしれませんが、こんな企業では問題になりませんよね。ところで、この最適ではない在庫管理方法にふさわしい名前をご存じですか?「在庫は善」方式でしょうか?
3. 予測モデルに基づいた動的発注点と安全在庫を併用する在庫注文システムの利用
平均化された販売数量を基礎とする古典的な仮定と同じように、考えうるパラメーターをすべて考慮した予測でも、その精度はせいぜい50-60%です。その排反である40-50%は安全在庫に依存しますが、安全在庫に依存している期間では、トレードオフの問題が再び発生します。安全在庫を減らせば収益が減り、安全在庫を増やせば維持管理費が増える問題です。
在庫最適化を適切に行うシステムを試してください
これまで説明してきたケースと全く違うことができるのかと、悩むかもしれません。以下はネタばれです。
在庫最適化を適切に行う手法が1つありますが、理解するにはしばらく時間がかかるかもしれません。この手法は、購入数量と購入サイクルのそれぞれが変動することを前提とします。これまでの失敗例は、どちらかが変動しない前提がありました。Min/Max在庫注文システムでは、購入数量が変動しません。発注間隔一定の在庫注文システムでは、その名の通り、購入サイクルが変動しません。この手法は、購入サイクルと購入数量の2つの変動を考慮することから始まります。実際の需要が計画とずれても、システムにはいつでも購入制約を満たすオーダー発行の準備をさせてください。システムが安定的に稼働しているとすれば、競合他社よりも低い在庫水準でかつ高いサービス率で業務運用できるようになります、そして競合他社よりもはるかに早く成長できます。
サプライチェーンの損失を抑えるためのより良い方法について学びます。
- 予測・計画・発注の業務効率 2倍
- 在庫切れを最大98%削減 となり、それに応じて収益も増加します。
- 過剰在庫 15-50%減少
- 在庫回転率 35%増加
クレジットカードは必要ありません。
追加トピック:
計画のために Excel での手作業にまだ頼っていますか?
今すぐ Streamline で需要と供給の計画を自動化しましょう。
- 95-99%+ の最適な在庫可用性を実現し、顧客の需要に一貫して応えることができます。
- 最大 99% の予測精度を達成し、より信頼性の高い計画と意思決定を実現します。
- 在庫切れが最大 98% 削減され、販売機会の損失と顧客の不満が最小限に抑えられます。
- 過剰在庫を最大 50% 削減し、貴重な資本と保管スペースを解放します。
- マージンを 1 ~ 5 パーセントポイント増加し、全体的な収益性を高めます。
- 1 年以内に最大 56 倍の ROI を実現し、最初の 3 か月で 100% の ROI を達成できます。
- 予測、計画、発注に費やす時間を最大 90% 削減し、チームが戦略的な活動に集中できるようにします。