প্রতিযোগী সমাধানগুলির মধ্যে Streamline কে আলাদা করে তোলে

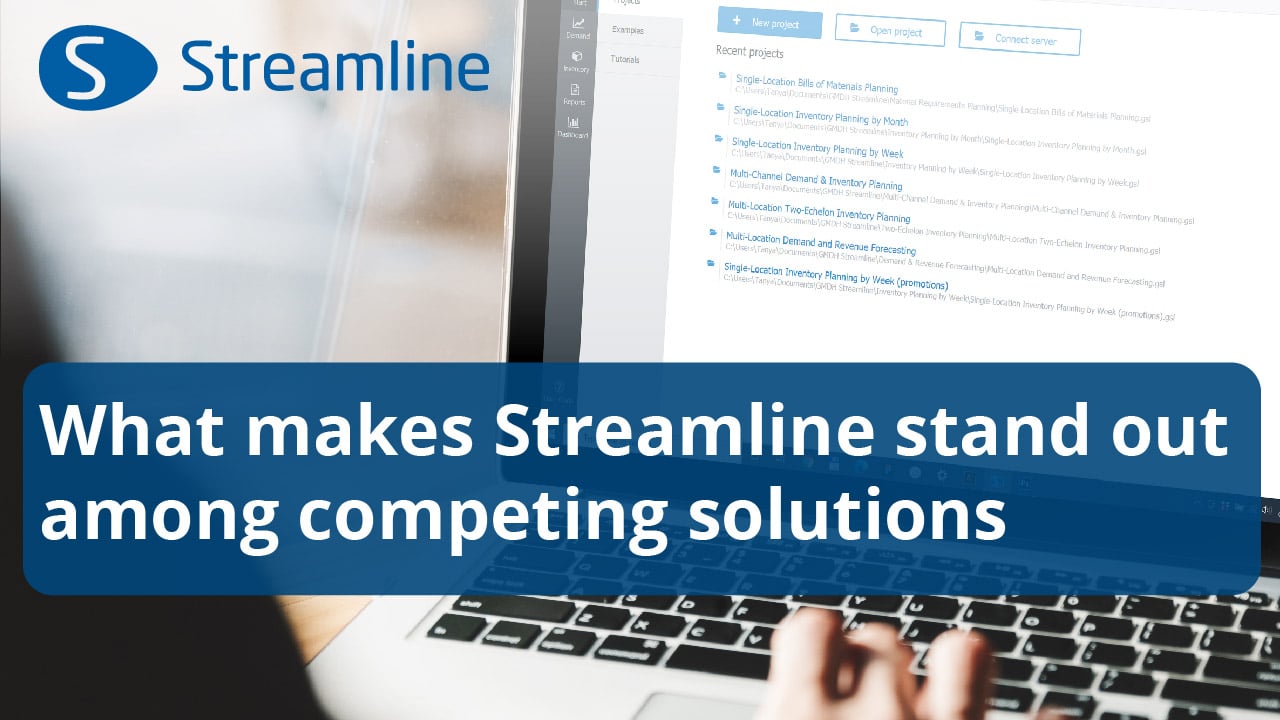
SKU জুড়ে অর্ডারের তারিখ সিঙ্ক করা হচ্ছে
আপনি কি করবেন যদি ইআরপি সিস্টেমে অন্তর্নির্মিত আপনার ন্যূনতম/সর্বোচ্চ পুনঃপূরণ কৌশল একটি SKU-এর জন্য ক্রয় সংকেত দেয় কিন্তু একই সরবরাহকারীর অন্যান্য SKU-এর এখনও পুনরায় পূরণের প্রয়োজন না হয়? ন্যূনতম/সর্বোচ্চ অর্ডার সংকেত আইটেম প্রতি আসে যখন ব্যবসা সরবরাহকারী প্রতি ক্রয় আদেশ জারি করে। তাই আপনি হয় সতর্কতা উপেক্ষা করুন এবং পরে একটি ঘাটতি হবে, অথবা অতিরিক্তভাবে একটি সম্পূর্ণ পাত্র ক্রয় করুন। ERP পদ্ধতির বিপরীতে, Streamline সরবরাহকারী প্রতি ক্রয়ের সংকেত বাড়ায়। Streamline একটি বিচ্ছিন্ন-ইভেন্ট সিমুলেশনের মাধ্যমে পরবর্তী অর্ডার চক্রের সময় সমস্ত ক্রয় সংকেত ভবিষ্যদ্বাণী করে এবং ধ্রুবক অর্ডার চক্রের সাথে একটি মসৃণ ক্রয় প্রক্রিয়া, বা সম্পূর্ণ পাত্রে ক্রয় করার জন্য (অর্ডার চক্র পরিবর্তনশীল), বা EOQ এর মাধ্যমে আগে থেকে কেনাকাটা করে৷
ডিসক্রিট-ইভেন্ট সিমুলেশন দিয়ে সূত্র প্রতিস্থাপন করা হচ্ছে
ইনভেন্টরি রিপ্লিনিশমেন্ট পরবর্তী লিড টাইমে এবং কখনও কখনও তার পরেও ভবিষ্যতের ইনভেন্টরি লেভেল গণনার উপর ভিত্তি করে। এর অর্থ হল আপনার সূত্রটিকে অসংখ্য আসন্ন খরচ এবং পুনরায় পূরণের ইভেন্টগুলির জন্য অ্যাকাউন্ট করতে হবে। কখনও কখনও এটি সম্ভব হয়, কিন্তু একবার আপনি একটি চালানের সময়সূচীর মতো ইভেন্টের সময়সূচী নিয়ে কাজ করা শুরু করলে বা ট্রানজিট Excel-এ একাধিক অর্ডার প্রায় সঙ্গে সঙ্গেই ছেড়ে দেয়।
যদিও আমাদের প্রতিযোগীরা সাধারণত ঘটনাগুলিকে বাস্তবসম্মতভাবে সংঘর্ষ না করে গণনাকে সহজ করে, Streamline একদিনের নির্ভুলতার সাথে একটি টাইমলাইন তৈরি করে এবং সমস্ত সময়সূচীকে টাইমলাইনে রাখে। তারপর Streamline ইভেন্ট সিকোয়েন্স চালায় যা আমাদের কোম্পানির ইনভেনটরি লেভেল সম্পর্কে এক দিনের নির্ভুলতার সাথে সবচেয়ে সঠিক তথ্য দেয়। কখনও কখনও এটি পুনরায় পূরণের সূত্রগুলির তুলনায় একটি আরও সঠিক পদ্ধতি, কিন্তু অনেক ক্ষেত্রে, এটি বাস্তব-বিশ্বের সরবরাহ চেইন জটিলতার জন্য মিটমাট করার একমাত্র উপায়।
চাহিদার পূর্বাভাস দিতে AI ব্যবহার করা
ঋতু, দামের স্থিতিস্থাপকতা বা টপ-ডাউন পূর্বাভাস অনুমান করা আজকাল যথেষ্ট নয়। বাজার খুব গতিশীলভাবে পরিবর্তিত হয় এবং আপনার বিক্রয়ের ইতিহাস বর্তমান পরিস্থিতির সাথে যথেষ্ট প্রাসঙ্গিক কিনা এবং ভবিষ্যতে এক্সট্রাপোলেট করতে ব্যবহার করা যেতে পারে কিনা তা অনুমান করা কঠিন। এটি এমন একটি ক্ষেত্র যেখানে আমরা আমাদের মালিকানাধীন AI ব্যবহার করি তাই আমরা শুধুমাত্র টাইম সিরিজের পূর্বাভাস কৌশল, ভবিষ্যদ্বাণী এবং স্তরের পরিবর্তনগুলি প্রয়োগ করি যদি AI বলে যে এটি প্রয়োগ করা উপযুক্ত – ঠিক যেমন আপনি প্রতিদিন প্রতিটি SKU-এর উপর নজর রাখছেন।
গ্রুপ EOQ
আপনি কি আপনার কাজে EOQ ব্যবহার করছেন? যদি তা না হয়, তাহলে এটি EOQ কে আরও ঘনিষ্ঠভাবে দেখার জন্য মূল্যবান কারণ এই ইনভেন্টরি প্ল্যানিং কনসেপ্টটি আপনার হোল্ডিং এবং অর্ডারিং খরচ উল্লেখযোগ্যভাবে হ্রাস করে। দুর্ভাগ্যবশত, ক্লাসিক EOQ SKU-এর জন্য গণনা করা হয় এবং SKU-এর একটি গোষ্ঠীর জন্য নয়। একটি বাস্তব-বিশ্ব সরবরাহ শৃঙ্খলে, ক্রয় আদেশে একাধিক SKU থাকে, যদি শত শত SKU না থাকে। যদিও Streamline ক্লাসিক EOQ গণনা সমর্থন করে, এটি গ্রুপ EOQও অফার করে যা একাধিক SKU অন্তর্ভুক্ত অর্ডারগুলির জন্য EOQ প্রযোজ্য করার ক্লাসিক পদ্ধতির বাইরে চলে যায়।
আইটেমগুলির একটি গ্রুপের জন্য অর্ডার তারিখ সিঙ্ক করার জন্য Streamline এর ক্ষমতার জন্য এটি সম্ভব হয়েছে৷ তারপর Streamline কেবলমাত্র SKU-এর গোষ্ঠীর জন্য সেরা অর্ডার চক্র খুঁজে পেতে সিঙ্ক্রোনাইজেশনের বাধাকে এগিয়ে নিয়ে যায় এবং স্বয়ংক্রিয়ভাবে হোল্ডিং এবং অর্ডারিং খরচের সমন্বয় কমিয়ে দেয়।
আপনি কি আপনার কোম্পানির ডেটাতে স্ট্রীমলাইন পরীক্ষা করতে চান?
কোনো ক্রেডিট কার্ডের প্রয়োজন নেই।
আরও পড়া:
- করোনাভাইরাস প্রাদুর্ভাবের সময় কীভাবে সাপ্লাই চেইন প্রক্রিয়াগুলি মোকাবেলা করবেন
- কেন Excel থেকে ইনভেন্টরি প্ল্যানিং সফ্টওয়্যারে স্যুইচ করবেন
- অবশ্যই পড়ুন: ব্যবসায়িক প্রক্রিয়া অপ্টিমাইজেশানের জন্য স্মার্ট সাপ্লাই চেইন ম্যানেজমেন্ট সমাধান
- সাপ্লাই চেইন প্ল্যানিং-এ ক্রস-ফাংশনাল অ্যালাইনমেন্ট: অ্যা কেস স্টাডি অফ সেলস অ্যান্ড অপারেশন প্ল্যানিং [পিডিএফ]
- চাহিদা ও সরবরাহ ব্যবস্থাপনা: সহযোগিতামূলক পরিকল্পনা, পূর্বাভাস এবং পুনরায় পূরণ
এখনও পরিকল্পনার জন্য Excel এ ম্যানুয়াল কাজের উপর নির্ভর করছেন?
স্ট্রীমলাইনের সাথে আজই চাহিদা এবং সরবরাহ পরিকল্পনা স্বয়ংক্রিয় করুন!
- গ্রাহকের চাহিদা ধারাবাহিকভাবে পূরণ করতে পারার বিষয়টি নিশ্চিত করে সর্বোত্তম 95-99%+ ইনভেন্টরি প্রাপ্যতা অর্জন করুন।
- 99% পূর্বাভাস নির্ভুলতা অর্জন করুন, আরও নির্ভরযোগ্য পরিকল্পনা এবং সিদ্ধান্ত গ্রহণ করুন।
- স্টকআউটে 98% পর্যন্ত হ্রাসের অভিজ্ঞতা, মিস করা বিক্রয়ের সুযোগ এবং গ্রাহকের অসন্তোষ কমিয়ে আনা।
- মূল্যবান পুঁজি এবং স্টোরেজ স্পেস খালি করে 50% পর্যন্ত অতিরিক্ত ইনভেন্টরি কাটুন।
- 1-5 শতাংশ পয়েন্ট দ্বারা মার্জিন বৃদ্ধি, সামগ্রিক লাভজনকতা বৃদ্ধি.
- প্রথম তিন মাসে অর্জনযোগ্য 100% ROI সহ এক বছরের মধ্যে 56 বার পর্যন্ত ROI উপভোগ করুন৷
- পূর্বাভাস, পরিকল্পনা এবং অর্ডার করার সময় 90% পর্যন্ত কমিয়ে দিন, আপনার দলকে কৌশলগত কার্যকলাপে ফোকাস করার অনুমতি দেয়।