亏损百万的3大方法优化库存
–
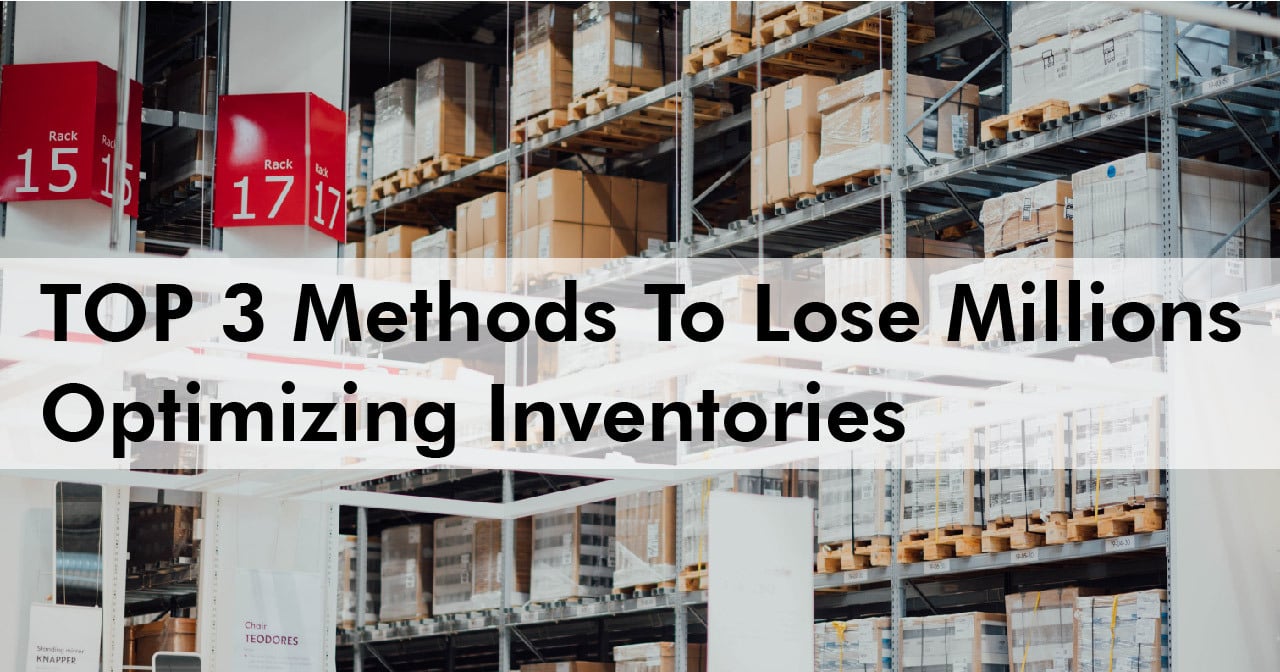
5分钟阅读
目录:
介紹
本文作者采访了500多家企业,他们同时抱怨库存短缺和库存过多。在他们的案例中,经典的库存补货策略在没有可行的原因下失败了。这是我们第一次分享我们关于经典库存优化方法出错的笔记,我们真的希望你会觉得无聊,因为你永远不会犯这些错误。
为了确保我们的观点是一致的,请注意,文章是针对供应链规划或运营方面的高管职位的。文章解释了库存计划人员如何应用经典策略管理库存,在没有明显原因的情况下,未能减少短缺或过多的库存。在对整个采购流程进行详细审核之前,请不要将任何过错延伸到你的库存计划和采购团队身上。
管理数千种产品或部件的企业总是在库存水平和服务水平的权衡中挣扎。你降低库存水平以减少账面成本,但这会拉低产品的可用性,反之亦然。
库存水平看似控制得很好,同时公司有一位在公司工作30年以上的库存补货大师,他预判了销售数据和会有好的趋势的商品,并成功利用经验法则生产出订单量。但迟早有一次外部审计发现,与行业内其他公司相比,库存周转率和填充率太差了。 于是公司决定实施一个闪亮的新的自动化库存补货系统,使用一堆被证明是行业标准的经典方法。
而在实施库存补货和优化系统3-6个月后,有什么惊喜会期待好60%的企业对库存进行评估后。他们最终还是回到了库存扭曲的起点,唯一的好处是系统让计划团队在大部分时间里都能冷静下来,但也不是每个实施案例都是如此。
那么,在常规的行业标准中,你应该怎么做,才能不可避免地重复这种令人沮丧的经历呢?这里列出了3大方法。
1.使用最小/最大库存订购系统
这是一个基本的库存计划系统,它往往是内置到您的ERP开箱即用。有很多关于这个策略是如何工作的信息 - 你可以很容易地找到许多手册和。 解释如何微调最小和最大级别的文章。.
只剩下一个问题,当某一产品或物料出现补货提醒时,您会在当天执行采购,还是等待几周后将这一产品与该供应商的所有其他产品同步,以最大限度地降低运输成本,满足供应商的最低采购要求?
如果你得到了这个问题,请你考虑一下。但这是个陷阱--都不行。从字面上看,你是在2周的缺货和未知时期的资本冻结之间做出选择。实际上,计划员在所有可能的组合中都会这么做--有些人立即采购,增加运输成本,造成库存过剩;有些人则在需要下一个大订单的时候忽略潜在的短缺。在后一种情况下,计划员在每个PO中给每个供应商制造不同产品的定期短缺。
有的企业从一开始就明白了Min/Max的问题,因此,宁愿用#2的方法输钱,也要用更复杂的方法。
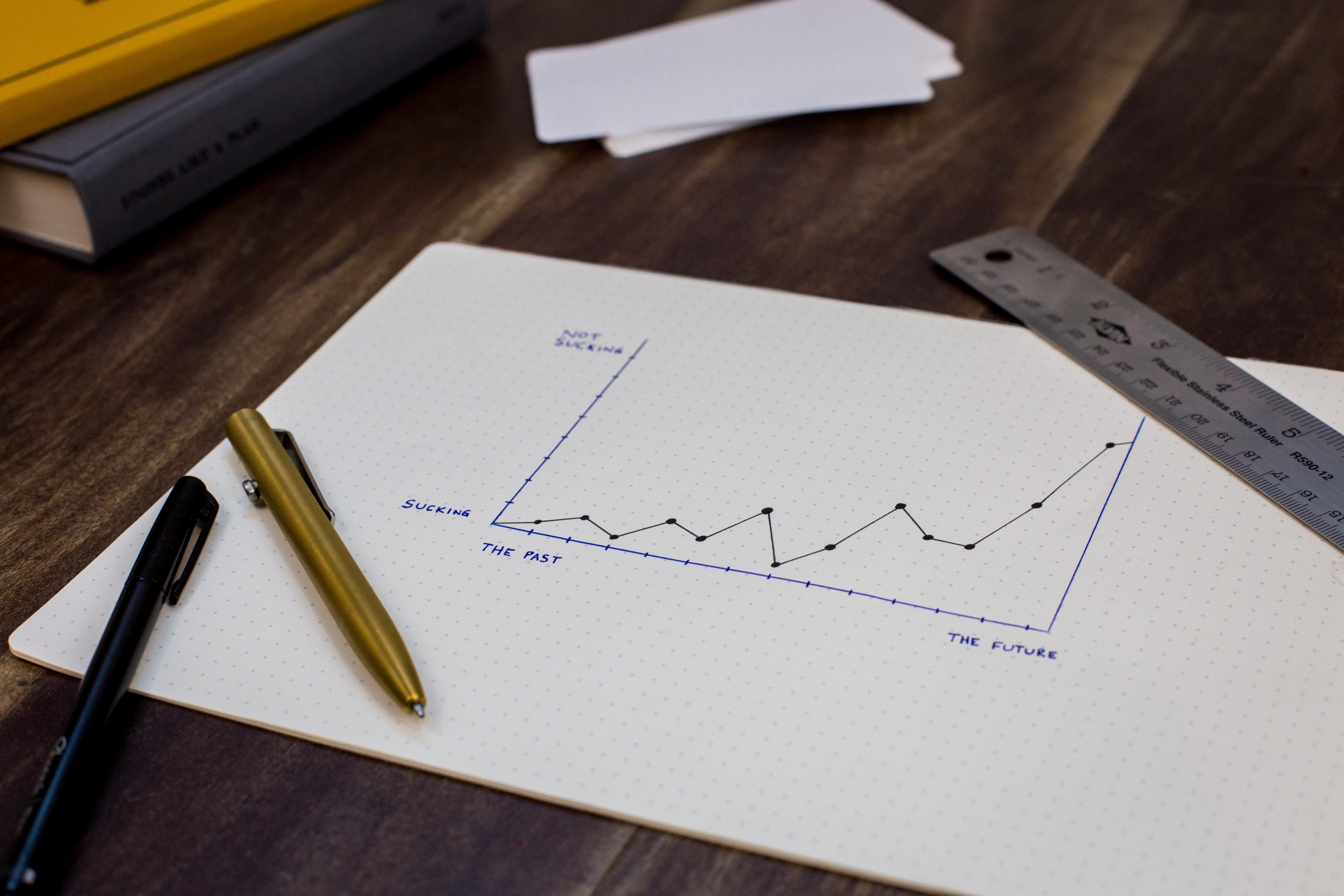
2.使用固定期重新排序系统
不久,这里我们将预选案例#1中的2周缺货方案。
让我来解释一下。固定的周期系统每个周期如一周或一个月触发一次PO。而这对于海外订购来说,似乎特别合理。但你猜猜看,那些销售速度比我们预期快的商品会发生什么?它们会被忽略,直到下一个周期,这很不幸。
哦,等等,也许有一个解决短缺的办法。有些公司建立了价值90天销售量的安全库存,以确保短缺不再发生。不管每年的账面成本会猛增几百万美元。那么这就是一种库存非优化,或者说这个定义是什么好呢?
3.根据预测模型使用动态复购点和安全库存
就像传统的基于平均销售额的假设一样,把所有可能的参数都计算在内的预测,不会给你带来比50-60%更接近的精度。这意味着40-50%的时间你会依赖安全库存,这又是一种权衡--当你减少安全库存时,你会损失收入,当你增加安全库存时,你会增加账面成本和冻结资本。又是同样的问题--公司优化库存,每年继续亏损几百万。
试用一个能正确进行库存优化的系统
你可能会想,到底有什么可以做的不一样呢?下面小编就给大家介绍一下。
是的,有一种方法可以正确地进行库存优化,不过你需要花一段时间来了解它。该方法首先要考虑可变的采购周期时间和可变的采购数量。有了这个方法的系统应该做好准备,如果实际需求数量突然与计划有较大差距,可以在任何一天发出满足采购约束的订单。如果系统运行稳定,不出现任何问题,你就可以在比竞争对手低得多的库存水平下运作,为客户提供更高的服务水平,并比竞争对手发展得更快。
了解供应链中更好的止损方法。
- 预测、计划和下单速度加倍。
- 减少多达98%的缺货 并相应增加收入。
- 减少多余库存15-50%。
- 提高库存周转率35%。
无需信用卡
进一步阅读:
Excel 中仍依赖手工进行规划?
立即使用 Streamline 实现需求和供应计划的自动化!
- 实现最佳的 95-99%+ 库存可用性,确保您能够始终如一地满足客户需求。
- 达到高达99%的预测精度,获得更可靠的规划和决策。
- 缺货情况减少高达 98%,最大限度地减少错失的销售机会和客户不满。
- 减少多余库存高达 50%,释放宝贵的资金和存储空间。
- 提高利润率1-5个百分点,提升整体盈利能力。
- 一年内可享受高达56倍的投资回报,前三个月可实现100%的投资回报。
- 将预测、计划和订购所花费的时间减少多达 90%,让您的团队专注于战略活动。